Table of Contents
LHD loaders, short for Load-Haul-Dump loaders, are essential machines in underground mining operations. Whether you’re navigating the tight tunnels of a coal mine or moving heavy ore in a metal mine, LHD loaders are the go-to solution. In this post, we dive deep into the world of LHD loaders, covering everything from major manufacturers to the key factors you should consider when choosing one for your operation. Let’s load up on some knowledge!
1. The Big Players in the LHD Loader Market
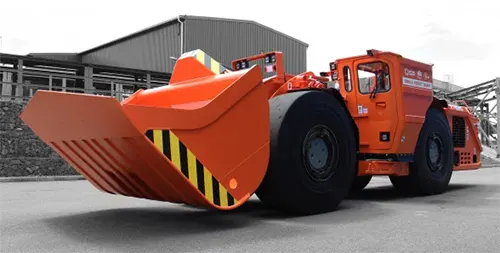
When it comes to LHD loaders, a few global giants dominate the market:
– Sandvik: A Swedish industrial giant known for high-quality, technologically advanced mining machinery. Sandvik’s LHD loaders are celebrated for their durability and efficiency.
– Caterpillar: An American powerhouse in construction and mining equipment, Caterpillar offers a variety of LHD loaders known for their power, reliability, and durability.
– Komatsu: This Japanese company is a major player, with LHD loaders that are competitive in both performance and quality, widely used in various mining and engineering operations.
– Epiroc (formerly part of Atlas Copco): Based in Sweden, Epiroc is known for efficient, energy-saving LHD loaders that are particularly popular in the mining industry.
– GHH-Fahrzeuge: A German OEM that offers LHD loaders with large buckets and compact designs, ideal for specific underground applications. Their LF-7 loader, powered by a Cummins diesel engine, is an excellent example of their commitment to high power and low emissions.
– CNR: CNR (Yantai NaRui) is a Chinese professional manufacturer of mining equipment, including LHDs (Load, Haul, and Dump; or underground loaders), underground mining trucks and other products related to mining.
2. Market Distribution: Who Needs LHD Loaders?
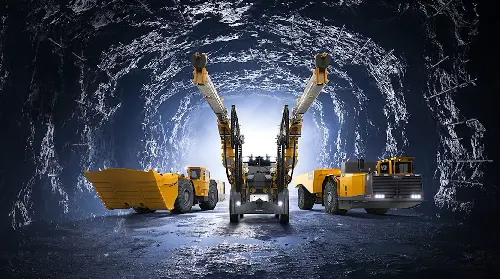
LHD loaders are indispensable in regions with significant mining activities:
– Mining-rich regions: Countries like Australia, Canada, and South Africa are key markets due to their vast mineral resources. In Australia, for example, LHD loaders are crucial for loading, transporting, and unloading ore in both metal and coal mining operations.
– Emerging economies: Countries such as China, India, and Brazil are ramping up their infrastructure development and resource extraction efforts. China’s extensive use of LHD loaders in coal mines, combined with increasing demand in metal mining, makes it a significant market. India and Brazil are also seeing a steady rise in demand as their mining industries expand.
– Europe: Countries like Sweden and Finland not only produce LHD loaders but also use them extensively in their advanced mining and construction sectors. The European construction industry also relies on these machines for various tasks.
3. Applications of LHD Loaders: Where Do They Shine?
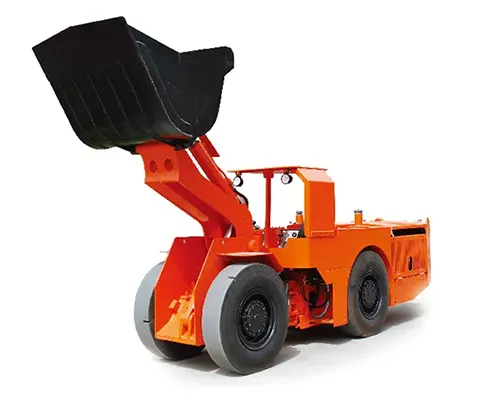
LHD loaders are versatile machines used in a range of underground and construction environments:
– Coal mining: These machines are perfect for underground coal extraction, handling tight spaces with ease. They transport coal from the extraction face to designated areas for further processing or lifting to the surface.
– Metal mining: In gold, copper, iron, and other metal mining operations, LHD loaders are critical for moving ore from the mining face to processing plants or storage areas. Their durability and load capacity make them ideal for harsh, complex environments.
– Tunnel construction: During tunnel excavation, LHD loaders efficiently remove debris and transport it out of the tunnel. They are commonly used in the construction of subways, highways, and water supply tunnels.
– Hydroelectric projects: In large-scale water projects, LHD loaders help with excavating the foundation for dams and moving materials during the construction of underground power plants.
– Underground infrastructure: Whether laying pipelines or building underground storage facilities, LHD loaders streamline material handling and transport, making these projects more efficient.
4. How to Evaluate the Performance of LHD Loaders
Selecting the right LHD loader involves evaluating several critical factors:
– Loading capacity: This depends on your operation’s needs. Larger buckets reduce the number of trips required, improving efficiency. However, bigger isn’t always better; you need to balance capacity with the machine’s size and the space available in your operation.
– Operational speed: Faster loaders mean quicker work cycles, which is crucial in projects where time is of the essence. However, faster speeds can come at the cost of higher fuel consumption.
– Powertrain: Most LHD loaders are diesel-powered, offering strong performance in rugged environments. Electric loaders are gaining popularity for their lower operational costs and environmental benefits, especially in regions with strict emission regulations.
5. Quality and Reliability: The Backbone of LHD Loaders
When investing in an LHD loader, quality and reliability are paramount:
– Manufacturer reputation: Opt for loaders from reputable manufacturers like Caterpillar, Sandvik, CNR, or Komatsu. These companies have a long history of producing reliable, high-quality machinery backed by strong after-sales support.
– Durability: Look for machines with robust construction, particularly in critical components like the bucket, frame, and transmission. High-strength, wear-resistant materials will ensure your loader stands up to the demands of mining operations.
– Maintenance costs: Consider the cost and availability of spare parts, the ease of maintenance, and the level of technical support available. Lower maintenance costs over the machine’s lifespan can offset a higher initial purchase price.
6. Comfort and Ease of Operation
Operator comfort and ease of use are often overlooked but critical factors:
– User-friendly controls: Choose loaders with intuitive controls that reduce operator fatigue and minimize the learning curve.
– Cabin comfort: A comfortable, ergonomically designed cabin with good visibility, climate control, and low noise levels can significantly enhance productivity. After all, happy operators are more productive operators!
7. The Bottom Line: Cost vs. Value
The price of an LHD loader varies widely depending on its size, features, and brand. However, a higher upfront cost can often translate into better value over the long term due to increased durability, lower operational costs, and better support.
– Entry-level loaders: Priced from a few thousand dollars, these are suitable for smaller operations with less demanding needs.
– Mid-range loaders: Typically ranging in the tens of thousands of dollars, these offer a balance between cost and performance, ideal for medium-sized mining and construction projects.
– High-end loaders: For large-scale operations, high-end loaders can cost hundreds of thousands of dollars but offer the best performance, durability, and after-sales support.
Conclusion
In conclusion, LHD loaders are a vital component in underground mining and construction operations. From the big-name manufacturers to the regions that demand them most, understanding the nuances of these machines can help you make an informed decision when purchasing one. Remember, it’s not just about the initial cost—consider performance, reliability, and operational costs to ensure you’re getting the best value for your investment.
So, next time you’re faced with the choice of an LHD loader, think of it as more than just a machine—it’s a key player in your operation’s success.