Table of Contents
Drill rigs are the backbone of underground mining and tunnel engineering, responsible for the precision drilling that allows these industries to thrive. But what exactly goes into making these machines tick? Let’s break down the key components, types, and trends that are shaping the future of drill rigs, with a focus on their role in modern mining operations.
1. The Structural Composition of Drill Rigs
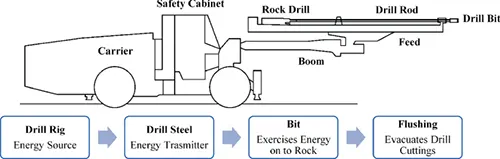
Drill rigs are robust machines designed to handle the tough underground environment. Here’s a look at their main components:
– Chassis: The foundation of any drill rig, the chassis supports the entire machine. Depending on the terrain, the chassis may be track-mounted or wheel-mounted. Track-mounted rigs offer superior stability and can traverse rough, uneven ground, making them ideal for large, complex mining operations. On the other hand, wheel-mounted rigs are more mobile and faster, suited for environments where speed and maneuverability are essential.
– Drill Arm System: The heart of any drill rig, the drill arm system, consists of multiple flexible and movable arms that position the drill bit with precision. These arms can extend, rotate, and pivot, allowing the drill to reach the exact spot where the hole needs to be drilled. Each arm is equipped with a drill machine that performs the actual drilling work.
– Drill Machine: The core of the operation, the drill machine, determines the efficiency and quality of the drilling. It operates by striking and rotating to break the rock, with various types, power levels, and impact frequencies available depending on the job’s specific requirements.
– Control System: Modern drill rigs come with sophisticated control systems that include electrical and hydraulic components. The electrical control system manages the rig’s electrical devices, such as motors, lights, and sensors. Meanwhile, the hydraulic system controls the movement of the drill arms, the operation of the drill machine, and the rig’s locomotion, ensuring precise control over pressure, flow, and direction.
– Power Unit: The powerhouse of the drill rig, the power unit, typically uses either a diesel engine or an electric motor. Diesel engines are preferred for their strength and adaptability in areas without a fixed power supply. Electric motors, however, are favored for their quiet operation, low emissions, and environmental friendliness, especially in regions with reliable electricity.
2. How Drill Rigs Operate
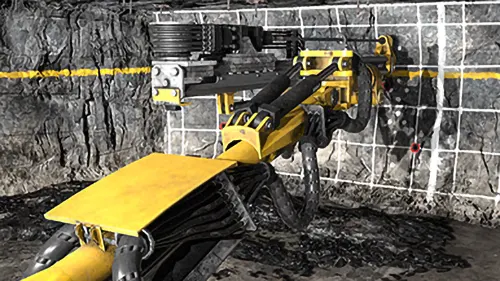
Operating a drill rig is a complex task that requires careful coordination of its various systems. Here’s a simplified overview of the process:
1. Positioning: The operator uses the control system to move the drill rig to the work site. The flexible drill arm system then aligns the drill machine with the intended drilling point.
2. Drilling: Once positioned, the drill machine is activated. The machine’s piston, driven by high-pressure oil or compressed air, delivers powerful impacts while the drill bit rotates. This combination of impact and rotation efficiently breaks the rock, creating a hole.
3. Adjustment: Throughout the drilling process, the operator may adjust the position of the drill arm and the drilling parameters to ensure accuracy and maintain quality.
4. Completion: After one hole is completed, the rig moves to the next drilling point, repeating the process until the entire drilling plan is fulfilled.
3. The Different Types of Drill Rigs
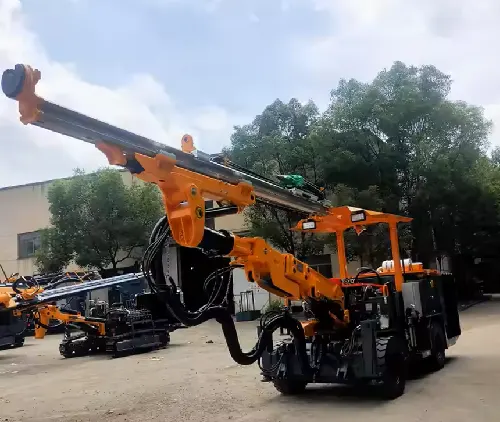
Drill rigs are classified based on their drilling method, movement system, and automation level. Let’s explore these categories:
– By Drilling Method:
– Down-the-Hole (DTH) Rigs: In DTH rigs, the drill bit works within the hole, driven by high air pressure. These rigs are known for their high efficiency and are capable of drilling deep holes, making them ideal for large-scale mining operations.
– Top Hammer Rigs: These rigs feature a drill bit that impacts the rock surface directly. While simpler and cheaper, they may not be as efficient or capable of drilling as deep as DTH rigs. They are more suitable for smaller mines or projects with less demanding requirements.
– By Movement System:
– Track-Mounted Rigs: Equipped with tracks, these rigs excel in stability and off-road performance, making them suitable for challenging environments. However, they tend to be slower and heavier, which can complicate transportation and setup.
– Wheel-Mounted Rigs: These rigs are faster and more agile, ideal for operations where quick movement between drilling sites is necessary. However, they require relatively even ground conditions and are less suited for rough terrain.
– By Automation Level:
– Manual Rigs: These require human operators to control all functions manually. While simpler and less costly, they demand skilled operators and result in higher labor intensity.
– Semi-Automatic Rigs: These rigs offer partial automation, allowing the machine to maintain certain drilling parameters automatically while the operator handles basic controls. This reduces labor intensity and improves efficiency and accuracy.
– Fully Automatic Rigs: These rigs automate the entire drilling process, including positioning, drilling, and rod changing. They require minimal human intervention, offering unmatched efficiency, precision, and consistency at a higher cost.
4. Applications of Drill Rigs
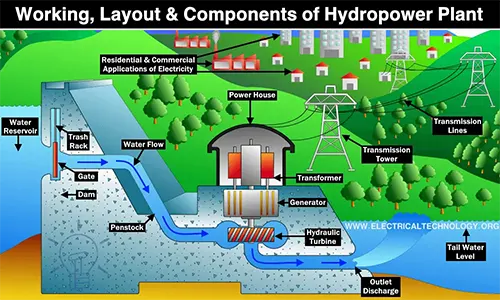
Drill rigs are indispensable in various sectors:
– Underground Mining: Drill rigs are used to create blast holes in underground mines, such as in iron, copper, and gold mining, allowing for efficient ore extraction. Their precision drilling capabilities optimize blasting results, maximizing ore recovery while minimizing environmental impact.
– Tunnel Engineering: In tunnel construction, whether for roads, railways, or subways, drill rigs are essential for drilling anchor and grouting holes, ensuring the stability and safety of the tunnel structure. Their adaptability to different tunnel shapes and sizes makes them invaluable in complex engineering projects.
– Hydropower Projects: Drill rigs play a crucial role in drilling grouting and anchor holes in hydropower projects, supporting the foundation treatment and structural construction of dams and underground powerhouses.
– Other Engineering Fields: Drill rigs are also used in defense projects, urban underground space development (e.g., parking lots, utility tunnels), and geological exploration, proving their versatility in any situation that requires rock drilling.
5. Market Trends and the Future of Drill Rigs
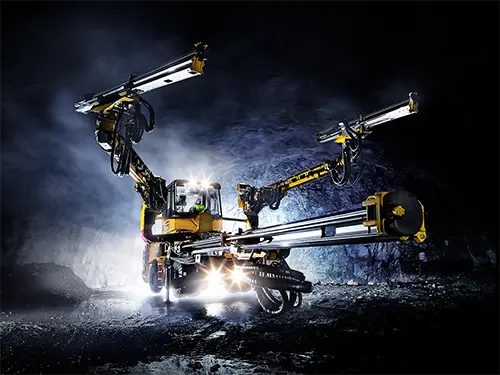
The future of drill rigs is shaped by technological advancements and changing market demands. Here are some trends to watch:
– Increased Automation and Intelligence: The push towards automation is leading to smarter drill rigs equipped with advanced sensors, AI algorithms, and control systems. These innovations enable automatic positioning, path planning, and parameter optimization, improving efficiency, accuracy, and safety.
– Polarization in Size: Drill rigs are evolving towards both ends of the size spectrum. On one hand, larger rigs are being developed to meet the demands of large-scale mining operations, offering greater power and drilling capacity. On the other hand, smaller rigs are gaining popularity in niche markets where flexibility, ease of use, and maneuverability are key.
– Green and Sustainable Design: Environmental concerns are driving the development of more eco-friendly drill rigs. Manufacturers are focusing on reducing emissions, energy consumption, noise, and dust generation, ensuring that these machines meet strict environmental regulations while minimizing their impact on both the operator and the surrounding environment.
– Multifunctionality: Future drill rigs may integrate additional functions, such as anchor installation, shotcrete application, and rock breaking, into a single machine. This multifunctionality increases equipment utilization, reduces the need for multiple machines on site, and cuts operational costs.
Conclusion
Drill rigs are essential tools in the mining and construction industries, offering precision, power, and versatility. As technology continues to advance, these machines are becoming smarter, greener, and more capable, ready to meet the challenges of the future. Whether you’re involved in underground mining, tunnel construction, or any other field that requires rock drilling, understanding the capabilities and trends of drill rigs will help you stay ahead in this rapidly evolving industry.