Table of Contents
When it comes to mining, moving massive amounts of rock, ore, and other materials is no easy task. Material transport in mining is a vital aspect of mining operations, and it’s a process that has evolved over time to meet the needs of increasingly large and complex mining projects. However, despite advances in technology, the industry still faces significant challenges. Let’s dive into some of the main issues and explore how miners are working to overcome them.
1. Material Handling Systems: The Backbone of Large Mining Operations
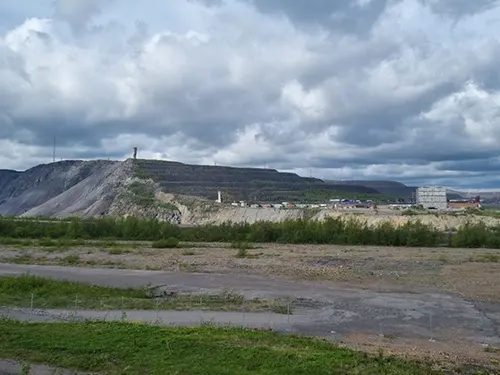
In large mining operations, particularly those dealing with massive block, panel, or sub-level caving mines like the Kiruna iron ore mine in Sweden, material handling systems (MHS) are essential. These systems are designed to efficiently move large quantities of ore from the mining face to the processing plant. However, they come with their own set of problems:
– Orepass Stability: Orepasses, the vertical or inclined shafts where ore is dropped to deeper levels, are prone to damage from the constant barrage of rocks. Over time, this leads to stress fracturing, which can result in blockages or even the collapse of the orepass.
– Haulage Level Deformation: The haulage level, where trains transport ore to the surface, is highly sensitive to deformation. Maintaining the stability of this level is critical to ensure the safe and efficient transport of materials.
To address these issues, mining companies are investing in more robust orepass designs and using advanced monitoring systems to detect early signs of instability. Additionally, regular maintenance and strategic reinforcement of the haulage level help to mitigate the risks associated with deformation.
2. Transporting Heavy Machinery and Equipment
Moving heavy machinery and equipment underground is another challenge. In deep mines, getting gear to the right location can be a logistical nightmare. Equipment is often loaded onto pallets, skids, or bins and transported by tractors with forks. However, this method is not without its pitfalls:
– Pierced Bags and Damaged Equipment: It’s common for bags of materials like dry shotcrete to be pierced by forklifts during transport. This not only results in wasted materials but also delays in operations.
– Lost Equipment: In some deep mines, it’s not uncommon for equipment to get lost in transit. Reordering lost items can cause significant delays and disrupt the workflow.
To combat these challenges, some mines are turning to technology, such as RFID tagging, to track equipment and materials as they move through the mine. While there are still issues with multiple tags interfering with each other, advancements in this technology are helping to reduce the incidence of lost or damaged goods.
3. The Tyranny of Tyres: A Big Problem for Big Trucks
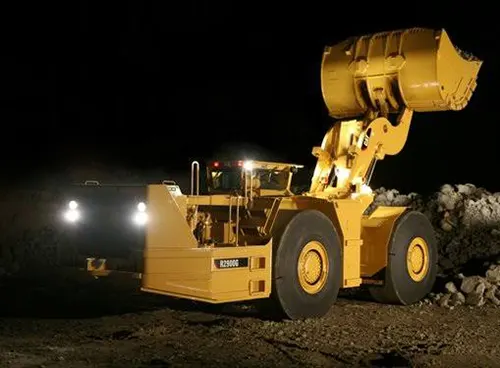
In many mining operations, especially in countries like Australia, large haul trucks are the workhorses of material transport. These trucks are capable of carrying massive loads, but they also come with their own set of challenges—particularly when it comes to their tyres.
– Heat Build-Up: High-speed, heavy loads, and uneven haul roads can cause tyres to heat up dangerously. This heat build-up can lead to rapid deflation or even tyre fires, both of which are extremely hazardous.
– Bias Loading: Poor loading practices, such as off-center weight distribution, can severely impact tyre performance. This not only increases wear and tear but also the likelihood of catastrophic tyre failures.
Mining companies are addressing these issues by improving haul road conditions, training operators in best loading practices, and investing in more durable tyre designs. Some are also exploring the use of autonomous vehicles, which can be programmed to follow optimal driving patterns that reduce tyre wear.
4. Environmental and Safety Concerns with Hazardous Materials
Mining operations often involve the transport of hazardous materials, both to and from the site. This adds another layer of complexity to material transport:
– TDG Certification: In many regions, drivers transporting hazardous materials require Transportation of Dangerous Goods (TDG) certification. This ensures that they are trained to handle these materials safely.
– GPS Tracking: To mitigate the risks associated with hazardous materials, some sites use GPS tracking to monitor the location and condition of these shipments. This is especially important for materials that pose significant environmental or safety risks if they are not handled properly.
– Moisture Content in Shipments: For materials transported by sea, such as refined products, the moisture content must be carefully monitored. If the moisture content is too high, it can cause the ship to capsize—a catastrophic event that miners are keen to avoid.
To improve safety and environmental outcomes, mining companies are increasingly turning to automation and remote monitoring technologies. These tools allow for real-time tracking and management of hazardous materials, reducing the potential for accidents and ensuring compliance with regulatory standards.
5. Innovation in Material Transport: The Future of Mining
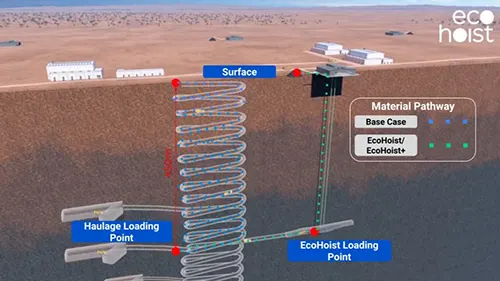
As mining operations become more complex and the demand for efficiency grows, innovation in material transport is becoming increasingly important. One area of focus is the electrification of transport systems:
– Trolley Assist Systems: Some companies are investing in trolley assist systems, which use overhead power lines to supplement the energy needs of haul trucks. This reduces the reliance on diesel and lowers greenhouse gas emissions.
– EcoHoist: Companies like EcoHoist are developing new methods for transporting materials from underground to the surface. These innovations are not only more energy-efficient but also offer greater safety and reliability compared to traditional methods.
– Autonomous Vehicles: The use of autonomous vehicles in mining is another exciting development. These vehicles can operate in harsh conditions without the need for human intervention, reducing the risks associated with material transport and increasing overall efficiency.
As these innovations continue to evolve, the future of material transport in mining looks promising. By embracing new technologies and improving existing practices, the industry is well on its way to overcoming the challenges that have long plagued mining operations.
Conclusion: Moving Mountains—Literally
Material transport in mining is a complex and challenging process, but it’s also one that’s critical to the success of mining operations. From orepass stability to tyre management, miners face a myriad of obstacles that require innovative solutions. By continuing to invest in new technologies and improving existing systems, the industry can look forward to a future where material transport is safer, more efficient, and more environmentally friendly.