Table of Contents
Tunnel boring machines (TBMs) are marvels of modern engineering, driving progress in everything from transportation tunnels to water management systems and mining operations. These machines have transformed how we approach massive underground projects, making them faster, safer, and more efficient. In this blog, we’ll dive deep into the world of tunnel boring machines, exploring their working principles, key components, and where they’re most commonly used.
1. How Tunnel Boring Machines Work: A Closer Look
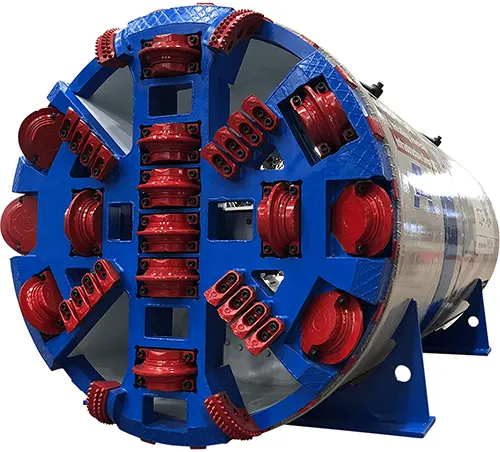
At the heart of a tunnel boring machine’s operation is the shield method. This technique allows TBMs to excavate tunnels through soil and rock while simultaneously providing support to prevent collapses, ensuring the stability of the tunnel as it is constructed. The machine’s rotating cutterhead is equipped with disc cutters and scrapers that grind away at the material ahead, breaking it down into manageable pieces.
As the cutterhead rotates, it continuously removes the excavated material, which is then transported through a conveyor system to be expelled from the tunnel. Simultaneously, the TBM installs lining segments to reinforce the newly created tunnel walls, ensuring long-term stability and safety.
2. The Core Components of a Tunnel Boring Machine
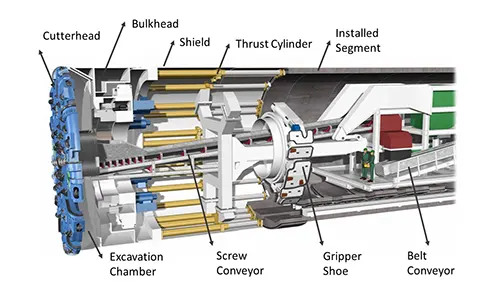
A tunnel boring machine is a complex system composed of several critical components that work together to achieve seamless tunneling. Here’s a breakdown of its key parts:
– Cutterhead: The cutterhead is the business end of the TBM, featuring a rotating disc equipped with cutting tools. These tools grind through rock and soil, breaking it down into smaller pieces. The cutterhead’s design varies depending on the type of ground it needs to excavate, whether soft soil, hard rock, or a mixture of both.
– Conveyor System: Once the material is excavated, it needs to be transported out of the tunnel. The conveyor system, which includes belts and muck cars, takes the broken material from the cutterhead and moves it outside the tunnel, maintaining a continuous flow to prevent backups.
– Propulsion System: The propulsion system, often hydraulic, pushes the TBM forward through the ground. Hydraulic jacks apply pressure to the rear section of the machine, enabling it to inch forward as excavation progresses. This system also ensures that the TBM remains stable and aligned throughout the process.
– Support System: As the TBM advances, it leaves behind a newly created tunnel. The support system ensures the tunnel’s stability by installing prefabricated concrete or steel segments that form the tunnel lining. This not only supports the tunnel walls but also creates a smooth interior surface.
3. Tunnel Boring Machines in Action: Real-World Applications
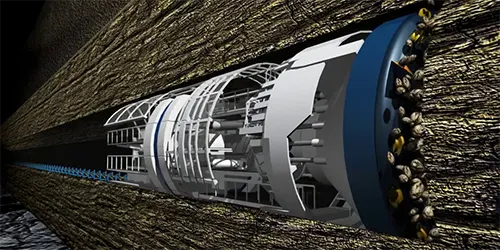
Tunnel boring machines are versatile and can be used in a variety of settings, making them indispensable in modern infrastructure development. Here are some of the most common applications of TBMs:
– Transportation Tunnels: TBMs are widely used to excavate tunnels for subways, highways, and railways. Whether it’s drilling through mountains or under cities, TBMs provide a safe and efficient way to construct transportation tunnels without disrupting surface activity.
– Water Management: TBMs play a crucial role in constructing tunnels for water conveyance and drainage systems. These include tunnels for water supply, sewage disposal, and flood control, where precise, large-scale excavation is required.
– Mining Operations: In the mining industry, TBMs are used to create access tunnels, ventilation shafts, and transportation corridors. Their ability to quickly and efficiently bore through hard rock makes them ideal for mining applications, significantly increasing productivity while reducing the need for manual labor.
4. The Advantages of Using Tunnel Boring Machines
The use of TBMs offers several advantages over traditional tunneling methods:
– Safety: By providing immediate structural support, TBMs reduce the risk of tunnel collapse and protect workers from hazardous conditions.
– Efficiency: TBMs can operate continuously, drastically reducing the time required to complete tunnel projects.
– Precision: Advanced guidance systems ensure that TBMs follow precise alignments, minimizing the risk of deviations and ensuring that tunnels meet their design specifications.
– Environmental Impact: TBMs minimize surface disruption, reducing the impact on the surrounding environment and communities.
5. The Future of Tunnel Boring Machines: Innovations and Trends
As technology advances, so too do the capabilities of tunnel boring machines. Future TBMs are expected to be even more efficient, capable of handling a wider range of geological conditions, and equipped with advanced monitoring systems to further enhance safety and precision. These innovations will continue to push the boundaries of what’s possible in tunnel construction, enabling even more ambitious infrastructure projects around the world.
Conclusion
Tunnel boring machines are more than just massive drills; they are engineering marvels that have revolutionized the way we approach large-scale underground construction. From transportation and water management to mining, TBMs have made it possible to build tunnels quickly, safely, and with minimal impact on the environment. As these machines continue to evolve, they will undoubtedly play an even more significant role in shaping the future of infrastructure.