Table of Contents
In the deep, dark recesses of the Earth where only the bravest machines dare to tread, the underground Load-Haul-Dump (LHD) machines are the unsung heroes. These mechanical workhorses dig, haul, and dump with a precision that has miners tipping their hard hats in respect. However, as the quest for deeper and more profitable mining ventures intensifies, so does the need for these machines to be smarter, faster, and safer. Enter autonomous LHD technology, the shining beacon of the future in underground mining. Let’s dive into the top five innovations that are shaping the next generation of LHDs.
1. Environmental Perception & 3D Modeling: Seeing in the Dark
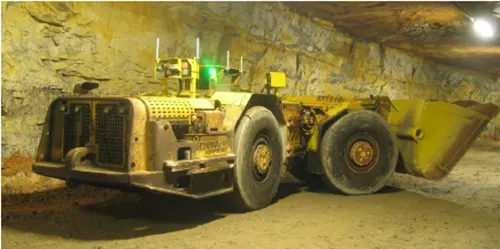
The first step to making a machine autonomous is teaching it to see. But let’s face it, it’s hard to see in the dark. That’s why the cutting-edge underground LHDs are equipped with a blend of sensors and cameras that allow them to create a detailed 3D map of their surroundings, even in the most dimly lit, dust-filled environments.
Traditional image sensors rely on good lighting, which is about as common in a mine as a canary singing opera. But with advances in distance sensors like LiDAR (Light Detection and Ranging) and TOF (Time of Flight) cameras, these machines can now gather data from their surroundings regardless of the lighting conditions. These sensors scan the environment and bounce back data that’s used to create a detailed 3D model of the terrain, including every rock, bump, and obstacle. It’s like giving the underground LHD a pair of high-tech night-vision goggles but without the cool green glow.
However, it’s not all smooth digging. While these sensors provide excellent data, they come with their own set of challenges. Image sensors, for example, struggle in dusty or obscured environments, which can lead to incomplete models and misguided digging attempts. On the other hand, distance sensors, while accurate, can slow down the processing time due to the sheer amount of data they collect. The future lies in finding the perfect balance between these technologies to create a system that is both fast and accurate.
2. Bucket Trajectory Control: The Perfect Dig
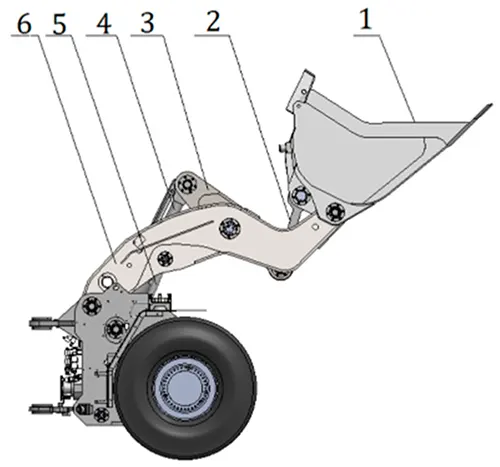
Controlling the bucket trajectory is like threading a needle while riding a bucking bronco. The goal is to ensure that every scoop is as efficient and effective as possible, minimizing energy consumption while maximizing load capacity. It’s a delicate dance between the machine’s force and the unpredictable nature of the underground environment.
There are two main approaches to this problem: force feedback control and learning-based control. The force feedback control method involves real-time adjustments based on the resistance the bucket encounters, much like how a human operator would adjust their digging based on feel. This method is excellent for dealing with uniform materials but can struggle with the varied and often chaotic underground environment.
On the other hand, learning-based control is where artificial intelligence shines. By analyzing past digging experiences, the AI can predict the best trajectory for the bucket to take, even in unpredictable conditions. It’s like having a veteran miner’s intuition embedded in the underground LHD. However, this method requires vast amounts of data and processing power, which can be a limiting factor in real-time operations.
3. Automatic Weighing Systems: No More Guessing Games
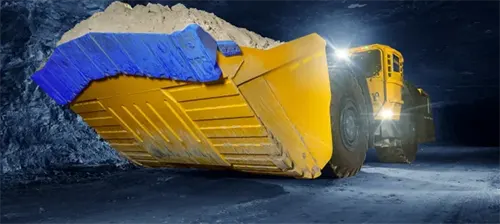
Knowing how much material is in the bucket of underground LHD is crucial for efficiency and safety. Automatic weighing systems are designed to measure the load in real-time, ensuring that each scoop is optimized for maximum efficiency. This system not only prevents overloading, which can be dangerous and damaging to the machinery, but also ensures that every trip is worth the fuel and time spent.
The challenge with these systems, however, is their adaptation to the underground environment. While ground loaders have been using automatic weighing systems for years, the technology has been slow to adapt to the harsh conditions of underground LHD mining. The need for robust and accurate systems that can withstand the dust, vibrations, and temperature extremes is driving innovation in this area.
4. Multi-Sensor Fusion: The Power of Teamwork
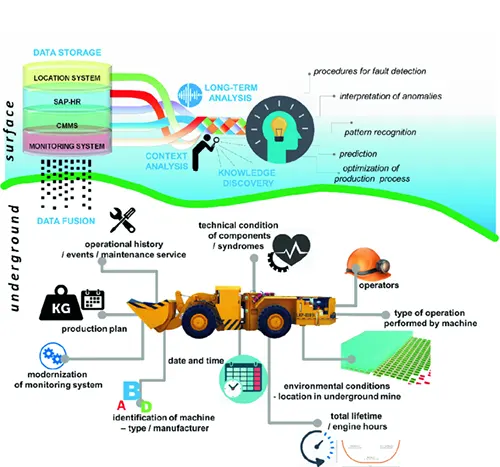
Why rely on one sensor when you can have them all working together? Multi-sensor fusion technology combines the strengths of various sensors to create a comprehensive view of the mining environment. This approach mitigates the weaknesses of individual sensors, such as the light dependency of image sensors or the slow processing of distance sensors.
By combining data from multiple sources, the underground LHD can make more informed decisions, leading to better trajectory planning, more accurate 3D modeling, and safer operations overall. It’s like having a team of experts all feeding into one brain, each one covering the other’s blind spots.
5. Reinforcement Learning & AI: Machines that Think
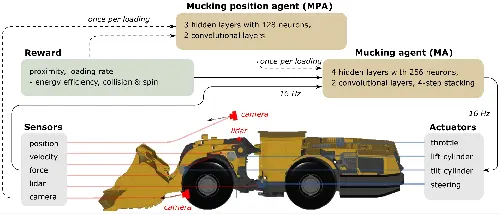
The future of underground LHDs is not just in seeing and reacting, but in thinking and learning. Reinforcement learning, a type of machine learning, allows these machines to learn from their experiences. Over time, an underground LHD can improve its efficiency, reduce its energy consumption, and increase its load capacity, all without a human having to lift a finger.
This technology is still in its infancy, but it holds incredible potential. Imagine an underground LHD that learns the layout of a new mine within hours, adapting its strategies to the specific challenges of the environment. It’s like having a robot miner that gets smarter with every load it hauls.
Conclusion: The Future of Underground LHDs
Autonomous LHD technology is not just a buzzword; it’s the future of underground mining. With advancements in environmental perception, bucket trajectory control, automatic weighing systems, multi-sensor fusion, and reinforcement learning, these machines are set to revolutionize the industry. They’re smarter, faster, and safer, paving the way for a future where underground mining is not only more efficient but also safer for the miners who work alongside these robotic powerhouses.
So the next time you think of mining, don’t just imagine pickaxes and canaries—think of cutting-edge technology and autonomous machines digging deeper, smarter, and with more precision than ever before.