Table of Contents
Underground loaders are the backbone of any efficient mining operation, especially in the deep, dark recesses of the earth where these mighty machines reign supreme. These workhorses are specifically designed to navigate the narrow, twisting tunnels and low-clearance environments typical of underground mining. But what makes these machines so essential, and how do they manage to operate so effectively in such challenging conditions? Let’s dig into six key aspects that define the underground loader.
1. Innovative Structural Design
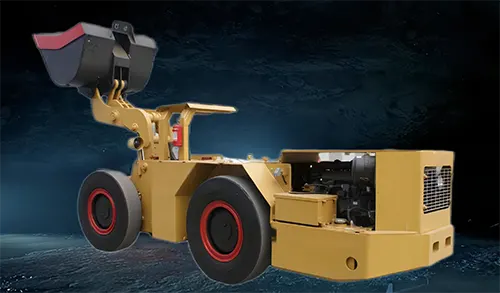
One of the most striking features of an underground loader is its low-profile design. With a squat, compact build, these loaders are tailored to squeeze through tight spaces that would make even a contortionist think twice. The low-slung body allows the machine to maneuver effortlessly through cramped tunnels and confined spaces, making it ideal for underground environments where height restrictions are common. Imagine trying to drive a double-decker bus through a McDonald’s drive-thru, and you’ll get a sense of the challenges these loaders overcome daily.
These loaders also boast a central articulation point, which enables them to turn on a dime—an invaluable feature when navigating the labyrinthine corridors of an underground mine. The articulated joint in the middle of the machine allows it to pivot, making sharp turns with ease. This level of agility is crucial in environments where one wrong move could mean getting stuck, or worse, causing a catastrophic accident. The underground loader is a master of tight turns and tricky spaces, ensuring it can handle whatever the mine throws at it.
2. Powered by Versatility
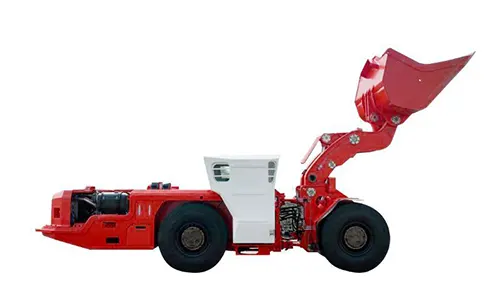
When it comes to powering an underground loader, you’ve got options, and each comes with its own set of advantages. Diesel engines are the most common power source, providing robust, torque-rich performance that’s perfectly suited to the demands of underground work. These engines are built to handle the heavy loads and tough conditions found underground, pushing the loader through muck and rubble with ease. Picture a bodybuilder lifting weights in a sauna, and you’ll get an idea of the strenuous conditions these diesel engines thrive in.
But in environments where ventilation is a concern—such as areas with high concentrations of flammable gases—electric motors come into play. These motors are powered by trailing cables and offer a quieter, cleaner alternative to diesel engines. Not only do they reduce the risk of fire hazards by eliminating exhaust emissions, but they also make the working environment more bearable for operators by cutting down on noise pollution. Think of the electric-powered underground loader as the silent but deadly ninja of the mining world.
3. How It All Works: The Nuts and Bolts
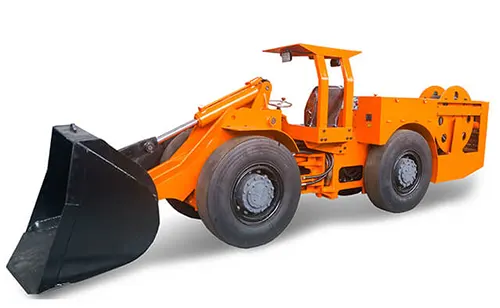
The operation of an underground loader is a marvel of engineering, powered by a combination of hydraulic systems and clever mechanics. The loader’s engine drives a hydraulic pump, which in turn powers the various functions of the machine, from lifting and tilting the bucket to driving and steering. When it’s time to scoop up some material, the operator lowers the bucket, digs into the pile, and uses hydraulic pressure to hoist the load. The bucket, located at the front of the loader, is the business end of the operation—capable of gathering, transporting, and dumping material with impressive efficiency.
Once the bucket is full, the underground loader trundles off to the designated drop-off point, where it flips the bucket to offload its cargo. This simple but effective process is repeated over and over, moving vast quantities of material from one place to another with minimal fuss. It’s like watching a well-oiled machine at work—because that’s exactly what it is. The hydraulics ensure smooth, precise movements, making the loader both powerful and easy to control, even in the most challenging conditions.
4. Applications: More Than Just Mining
While the underground loader is most commonly associated with mining, its utility doesn’t stop there. These machines are also indispensable in tunnel construction projects, where they’re used to clear debris and transport construction materials. Whether it’s carving out a new subway line or constructing a road tunnel through a mountain, the underground loader plays a pivotal role in ensuring the project stays on track.
In mining, these loaders are the go-to for handling everything from ore and waste rock to soil and rubble. Whether it’s a gold mine, a coal mine, or even a salt mine, you’ll find an underground loader hard at work, day in and day out. These machines are the unsung heroes of the mining industry, performing the heavy lifting so miners can focus on extracting valuable resources from the earth.
5. Built for the Toughest Environments
The underground loader is engineered to withstand the harsh conditions found underground. From extreme humidity and dust to the ever-present risk of explosive gases, these loaders are built to survive and thrive where lesser machines would crumble. Dust-proofing, waterproofing, and explosion-proofing are just some of the features that make these machines tough enough for the job.
In addition to their rugged construction, underground loaders are also designed with safety in mind. After all, when you’re operating heavy machinery in a confined space miles below the earth’s surface, safety is paramount. These machines are equipped with advanced safety features, including reinforced cabins, emergency shutoff systems, and specialized lighting to ensure the operator can see clearly in the dimly lit tunnels. With these features, the underground loader becomes not just a machine, but a trusted partner in some of the world’s most dangerous work environments.
6. Safety and Operation: A Balancing Act
Operating an underground loader is no job for the faint of heart. It requires a skilled operator who understands the machine’s capabilities and limitations, as well as the unique challenges of working underground. Before getting behind the controls, operators undergo extensive training to learn how to safely maneuver the loader, operate the hydraulic systems, and navigate the complex underground environment.
Routine safety checks are also a critical part of operating an underground loader. Before each shift, operators are required to inspect the machine, checking everything from tire pressure and brake functionality to the condition of the hydraulic hoses and electrical systems. It’s a bit like a pilot conducting a pre-flight check, only instead of soaring through the skies, these operators are delving into the earth’s depths.
Once the machine is up and running, maintaining a safe speed is crucial. Underground tunnels can be narrow and winding, with limited visibility and unexpected obstacles at every turn. That’s why underground loader operators are trained to keep their speed in check, especially when navigating sharp turns or steep inclines. Safety protocols also dictate that operators maintain a safe distance from other equipment and personnel, reducing the risk of collisions in these confined spaces.
Conclusion
The underground loader is an indispensable tool in the world of mining and tunnel construction, combining power, agility, and safety in a compact, rugged package. Whether it’s navigating tight spaces, handling heavy loads, or operating in hazardous conditions, these machines are built to get the job done efficiently and safely. By understanding the unique features and capabilities of the underground loader, we can better appreciate the vital role these machines play in keeping our mines and tunnels running smoothly. So next time you hear the term underground loader, remember—you’re talking about one of the true workhorses of the industrial world, a machine that’s as tough as the rocks it moves.